Unleashing the Potential of China CNC Precision Machining
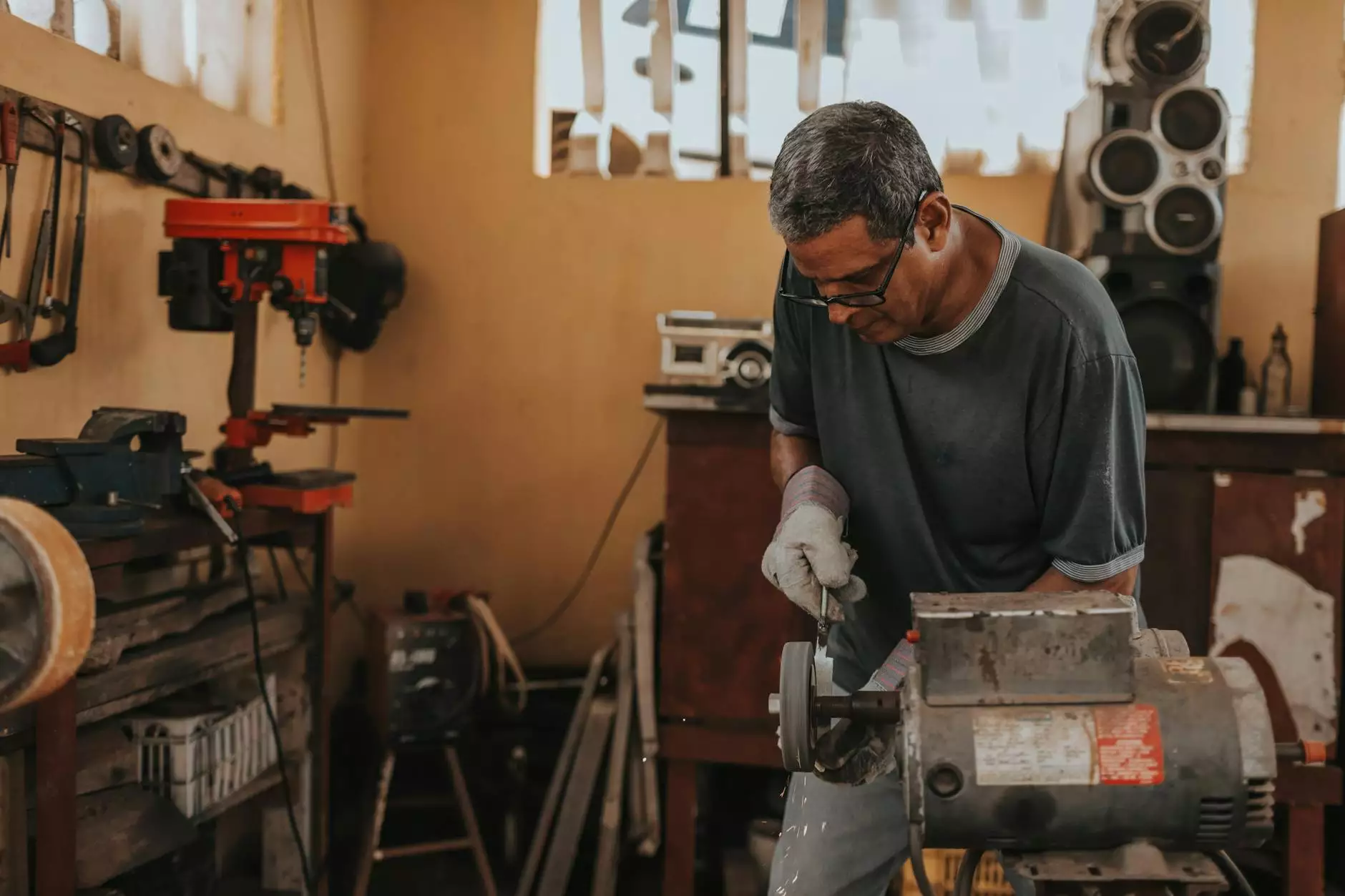
The landscape of modern manufacturing is constantly evolving, with advancements in technology reshaping how products are designed and constructed. Among the most significant innovations in this arena is China CNC precision machining. This method not only enhances the precision and efficiency of metal fabrication but also opens up a world of possibilities for industries ranging from aerospace to automotive. In this article, we explore the intricacies of CNC machining in China, its benefits, processes, technologies, and future trends.
Understanding CNC Precision Machining
CNC stands for Computer Numerical Control, a technological advancement that has revolutionized machining processes. In simple terms, CNC machines are automated tools that utilize computer programming to control the movement of machinery and tools. This ensures unmatched precision in producing a wide range of components and parts. China has emerged as a global leader in this field, showcasing an impressive blend of skilled labor, advanced technology, and cost efficiency.
The Role of CNC Machining in Metal Fabrication
CNC precision machining is a cornerstone of the metal fabrication industry. It involves various processes such as milling, turning, and grinding to transform raw materials into finished products. Here's a breakdown of how CNC machining collaborates effectively within the realm of metal fabrication:
- Milling: This process involves the removal of material from a workpiece using rotary cutters. CNC milling machines can produce complex shapes and designs with high accuracy.
- Turning: In this operation, the workpiece rotates while a cutting tool removes material. CNC turning is essential for creating cylindrical parts.
- Grinding: This finishing process ensures that surfaces are smooth and meet stringent tolerance requirements by removing small amounts of material.
Advantages of China CNC Precision Machining
As the manufacturing world leans more towards automation and efficiency, the advantages provided by China CNC precision machining become increasingly apparent:
1. Enhanced Precision and Accuracy
One of the most significant benefits of CNC machining is its ability to create highly precise and accurate parts. The computer-controlled nature of CNC machines minimizes human error and ensures products are made to exact specifications.
2. Cost Efficiency
China's robust infrastructure and skilled labor force contribute to lower production costs. Companies that utilize CNC machining benefit from lower overheads without sacrificing quality.
3. Complex Designs Made Possible
CNC machining allows for the creation of intricate designs that would be almost impossible to achieve with traditional methods. This capability has opened new avenues for innovation in product design.
4. High Production Rates
With the ability to run machines continuously and replicate designs with precision, CNC machining significantly increases production rates. This ensures faster turnaround times for projects and helps meet market demands efficiently.
5. Flexibility and Versatility
CNC machines can be programmed to handle multiple tasks, making them versatile for various applications in metal fabrication. Whether it is for a small prototype or a large production run, CNC machining can adapt accordingly.
The Processes Involved in CNC Precision Machining
Understanding the processes involved in CNC precision machining is vital for grasping its significance in the manufacturing sector. Here are the key steps:
1. Design and Programming
The process begins with designing the component using CAD (Computer-Aided Design) software. Once the design is finalized, it is converted into a format that CNC machines can understand, often using CAM (Computer-Aided Manufacturing) software to generate G-code.
2. Setup
The next step involves preparing the CNC machine, including securing the workpiece and customizing the machine settings to fit the specific job requirements.
3. Machining
This is the core phase where the CNC machine executes the programmed instructions, shaping the workpiece accurately according to the design.
4. Quality Control
Upon completion, the finished product undergoes a rigorous quality control process. Inspections ensure that the components meet all specifications and tolerances.
5. Finishing
The final step often involves additional finishing processes such as anodizing, coating, or polishing, enhancing the product’s appearance and durability.
Technological Advancements in CNC Precision Machining
As technology continues to evolve, so does CNC machining. Some of the latest advancements driving the industry forward include:
1. Automation and Robotics
The integration of robotic systems with CNC machines allows for higher levels of automation, reducing the need for manual intervention and increasing production efficiency.
2. 5-Axis Machining
5-axis CNC machining provides unparalleled flexibility in producing complex geometries, allowing for the machining of parts from multiple angles in one setup.
3. Cloud Computing and IoT
With the advent of the Internet of Things (IoT), CNC machines can be monitored and controlled remotely. This connectivity ensures real-time data analytics, improving operational efficiencies.
4. Advanced Materials
Modern CNC machining now accommodates a wider range of materials, including high-performance alloys and composites, enabling industries to innovate without limitations.
Challenges and Solutions in CNC Precision Machining
While CNC precision machining offers numerous advantages, some challenges must be addressed:
1. High Initial Investment
Investing in CNC machinery can be capital-intensive. However, the long-term returns through increased efficiency and lower operational costs often justify the expense.
2. Skill Gap
There is a growing need for skilled professionals capable of operating CNC machines. Companies can invest in training programs to bridge this gap, ensuring their workforce remains competitive.
3. Maintenance and Downtime
Regular maintenance is crucial for CNC machines to ensure they operate at peak performance. Establishing maintenance schedules can mitigate downtime and extend the lifespan of the equipment.
The Future of CNC Precision Machining in China
Looking ahead, the future of China CNC precision machining appears bright. With continued investments in technology and skilled labor, China is poised to maintain its position as a leader in global manufacturing. The following trends are expected to shape the future landscape:
1. Increased Customization
As industries demand more tailored solutions, CNC machining will adapt to provide highly customizable products, responding to unique client specifications.
2. Sustainability Efforts
With a growing focus on sustainability, CNC manufacturers are exploring ways to reduce waste and enhance energy efficiency in their operations.
3. Integration of Artificial Intelligence
AI is set to further innovate CNC machining processes, optimizing production workflows and predicting maintenance needs through data analysis.
Conclusion
In conclusion, China CNC precision machining represents a pivotal force in the manufacturing sector, driving efficiency, accuracy, and innovation. As industries continue to evolve, the importance of CNC technology and its applications in metal fabrication will only grow. Companies like deepmould.net play a crucial role in this landscape, leveraging cutting-edge techniques and skilled craftsmanship to deliver exceptional results. By embracing the advantages of CNC machining, businesses can not only enhance their production capabilities but also thrive in an increasingly competitive marketplace.